Fotos: Labsolda
Liga de cobalto em pó: 40 euros por quilo. Esse é o desafio de Jair Carlos Dutra em seu projeto de desenvolvimento de ligas para o reparo da erosão por cavitação em turbinas hidráulicas. O tipo de liga necessário – de morfologia esférica – para o projeto do Labsolda em parceria com a Tractebel e a Aneel ainda não é feito no país e o preço do produto importado para a pesquisa é, em média de 40 euros, por quilo, o item mais caro (36 mil reais) de um orçamento - 8,7% do total.
O projeto que Jair coordena no Labsolda - Laboratório de soldagem do curso de Engenharia Mecânica da UFSC - tem como título: “Desenvolvimento de Ligas Específicas e Tecnologias em Soldagem a Plasma com Pó Metálico para Aplicação em Regiões de Turbinas Hidráulicas Sujeitas à Erosão por Cavitação”.
A parceria do laboratório com a empresa geradora de energia, Tractebel, é antiga. A primeira patente registrada pela UFSC foi de uma tecnologia para recuperação de turbinas de usinas hidrelétricas, desenvolvida em 1997.
Atualmente, o projeto lida com o processo de erosão por cavitação em turbinas hidráulicas de grande porte. A passagem da água vai desgastando o metal das turbinas e é necessário, a cada quatro anos, reforçar o material. Esse processo requer o desligamento dos equipamentos e é feito manualmente. Para otimizar o processo, a equipe do Labsolda busca outra forma de reparo.
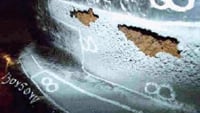
Cavitação em turbinas
O projeto compreende 3 linhas de pesquisa: o material usado na soldagem, técnicas de soldagem e a análise das variáveis do processo, que precisam ser consideradas para uma maior eficácia.
Material
O cobalto é o principal elemento das ligas utilizadas para reparo da cavitação. O produto é utilizado em pó e é fácil de ser misturado com outros componentes para se obter resultados específicos, mas seu custo é muito elevado. Um dos desafios dos pesquisadores é diminuir a quantidade de cobalto usado. Para isso o laboratório testou misturas com ferro, manganês e cromo.
A maior produtividade do produto em pó, que tem maior taxa de fusão, foi um fator determinante para os pesquisadores decidirem utilizar essa tecnologia. Além disso, em comparação com o arame, usado atualmente, há menor desperdício de material, logo, menos poluição.
Diante dos altos custos de importação o Labsolda está desenvolvendo as fórmulas mais adequadas de liga e pretende, em parceria com a Brats, fabricar o material no país e diminuir, assim, taxas de importação.
Na usina
O soldador usualmente realiza sua função em pé. No entanto, nas usinas hidrelétricas, diante das turbinas, essa posição é desfavorável ao processo. Um dos pontos inéditos da pesquisa realizada no Labsolda é a adaptação da soldagem para que o soldador possa realizá-la deitado, embaixo da turbina.
Com a energia gasta na soldagem, o material tende ao estado líquido. Neste caso, há o perigo de que o líquido caia no soldador. Para evitar isso, os pesquisadores do Labsolda desenvolveram um processo de pulsação – a carga de energia varia. Ou seja, a diminuição de energia impede que o material derreta e escorra. Logo em seguida, o aumento da energia mantém o processo de soldagem.
Outra adaptação necessária para a soldagem nessa posição é o desenvolvimento de um mecanismo que leve o pó para cima, o que também está em estudo.
Aplicação
Em julho de 2011, o projeto deve ser concluído. Tema da tese de doutorado do pesquisador Régis Henrique Gonçalves e Silva, já há desdobramentos que rendem outras pesquisas. “Foi o Labsolda que desenvolveu a tecnologia atual usada pela Tractebel para lidar com a cavitação ainda nos anos 90. Temos este projeto agora e planejamos, no futuro próximo, realizar a automatização do processo que por enquanto é feito manualmente”, diz Régis.