A ideia deste artigo é termos um pouco mais para discutirmos sobre os métodos de planejamento e, quem sabe, ajudar você a descobrir qual pode estar mais adequado ao seu processo produtivo. Para isso colocamos uma breve descrição dos tipos mais populares de planejamento.
No meu artigo anterior, chamado "Estoque: o terror que existe em todas as fábricas. Como minimizar?" eu firmei um comprometimento com vocês. Só para relembrar o comprometimento que fiz, vamos rever a última frase do artigo:
"Seria muito legal se vocês descrevessem como é na suas fábricas para debatermos sobre os métodos. No próximo trago uma breve descrição de cada método citado para não furar o acordo com vocês."
Então estou aqui entregando o prometido no artigo sobre "Estoques". Vou então fazer uma breve descrição dos métodos citados no artigo.
A ideia seria termos um pouco mais de informação para discutirmos sobre os métodos de planejamento e, quem sabe, ajudar você a descobrir qual pode estar mais adequado ao seu processo produtivo.
Então, lá vamos nós! Seguem abaixo as breves descrições dos métodos citados:
- Capacity Planning: Muitos sistemas de planejamento utilizam este método. Define a capacidade da planta num mundo teórico e perfeito, baseado primeiramente nas capacidades de cada máquina/recurso que representam as taxas de produção dos processos envolvidos. Por exemplo, 100 pessoas trabalhando 40 horas fornecem 4000 horas de capacidade. Então, comparando a atual demanda através de um calendário mestre com a capacidade da planta é possível estipular se as metas podem ser cumpridas ou não. Esse procedimento é conhecido como planejamento por capacidade infinita e assume-se que o chão de fábrica pode suprir a demanda alterando-se a capacidade.
- Finite Scheduling: Este método de planejamento é mais específico no sentido de alocar trabalho para cada recurso disponível. Ao examinar as etapas necessárias na execução de cada ordem de produção e padrões de tempo associadas as mesmas é possível organizar o uso de cada recurso e considerar que a capacidade é limitada no tempo. Ou seja, é um método mais realista porque entende quanto pode ser produzido num período de tempo considerando as restrições nos recursos produtivos.
- Forward Scheduling: Nesta alternativa o agendamento é feito a partir de datas iniciais estipuladas para uma operação e, então, é computado uma data final. A data inicial agendada é geralmente a data mais próxima disponível para a operação. Por exemplo, eu sei que para fazer 1.000 peças em uma determinada máquina (operação) leva 1 dia. Portanto, se eu encontrar um espaço na agenda para começar amanhã às 7 horas da manhã, eu sei que no dia seguinte às 7 horas da manhã isto estará pronto.
- Backward Scheduling: Funciona como o método acima, porém é dado como entrada ao sistema a data limite de entrega da operação e então é computado a data de início necessária. Usando também o exemplo acima, eu sei que para fazer 1.000 peças em uma determinada máquina (operação) leva 1 dia. Portanto, se eu preciso entregar ainda hoje, eu sei que já estou atrasado. E eu sei que para terminar amanhã às 7 horas da manhã eu preciso começar hoje no máximo até às 07 horas da manhã.
- Line Balancing: Neste caso, as tarefas são estipuladas para cada estação de trabalho de forma a minimizar a quantidade de estações de trabalho necessárias e o tempo ocioso dessas máquinas dado a atual necessidade de produção. A ideia é que cada operação tenha taxa de produção similar (ou balanceada), evitando gargalos, buffers e tempo ocioso em operações que são mais rápidas que as demais. Um processo produtivo assim é mais previsível, portanto, planejável.
- Sequencing: Este método na verdade é um componente do processo de agendamento que atua individualmente nas ordens de produção para determinar a fila (sequência) dos trabalhos em cada estação de trabalho. O sequenciamento, por sua vez, pode ser feito de diversas maneiras. Pode ser automático, levando em consideração regras e pesos pré-determinados, ou pode ser manual. Também é comum encontrar uma mescla, onde é feito o sequenciamento automático por um sistema, mas um ajuste fino é feito manualmente.
Eu, particularmente, simpatizo muito com a questão do sequenciamento, se for possível ele ser calculado automaticamente melhor. Entendo que muitas vezes não é possível e o ajuste fino manual no chão de fábrica pode ser necessário, mas para mim é um método que mais me parece interessante e vejo que é bem utilizado pelas fábricas que visito.
E vocês? Qual método você acredita ser mais adequado? Não esqueça de dizer a razão e em que tipo de processo produtivo.
Obrigado e até o próximo!
O conteúdo e a opinião expressa neste artigo não representam a opinião do Grupo CIMM e são de responsabilidade do autor.
Gostou? Então compartilhe:
Patrocinador:
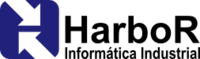
Tulio Duarte
O autor é formado em Ciências da Computação pela UFSC onde também cursou mestrado. Trabalha desde 2002 na HarboR Informática Industrial, empresa que desenvolve soluções para controle de produção e controle de qualidade. Neste período atuou em mais de 100 projetos de controle de produção e controle de qualidade para indústrias de todos os portes do Brasil e de outros países como Canadá, Estados Unidos, México, Colômbia, Chile, Uruguai, França, Itália, Eslováquia e China. É também co-fundador e atual presidente do grupo Vertical Manufatura da Acate, um grupo que aproxima empresas de tecnologia e indústria de manufatura para discutir e desenvolver soluções que visam a diminuição de custos, aumento de qualidade e produtividade, assim como o cumprimento de normas legais e diminuição de recalls.
Mais artigos: